Complete Guide to Defoamers: Applications, Benefits, and Solutions
Defoamers, also known as antifoaming agents, are chemical additives used to reduce and prevent the formation of foam in industrial processes.Foam can cause problems such as decreased efficiency, product contamination, and equipment damage.
Importance of Foam Control
Foam control is crucial in industries like wastewater treatment, paper manufacturing, food processing, and oil and gas.
Excessive foam can disrupt processes, lead to safety hazards, and affect product quality.
Foam Creation and Chemical Control
Foam is created when gas is dispersed in a liquid, forming bubbles stabilized by surfactants.
Defoamers work by disrupting the surfactant-stabilized bubbles. They spread rapidly across the foamy surface, destabilize the foam film, and cause the bubbles to collapse.
Importance of Foam Control
Foam control is crucial in industries like wastewater treatment, paper manufacturing, food processing, and oil and gas.
Excessive foam can disrupt processes, lead to safety hazards, and affect product quality.
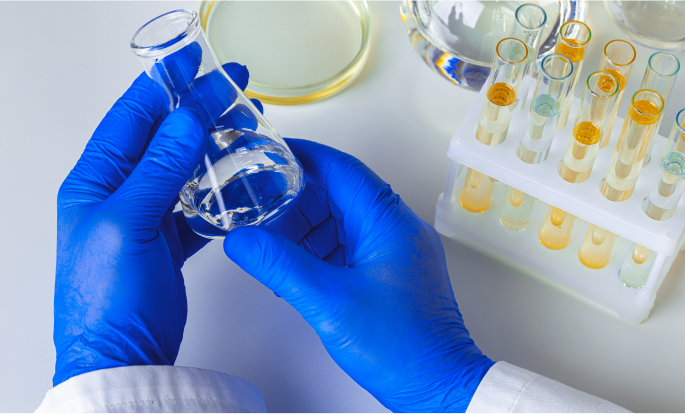
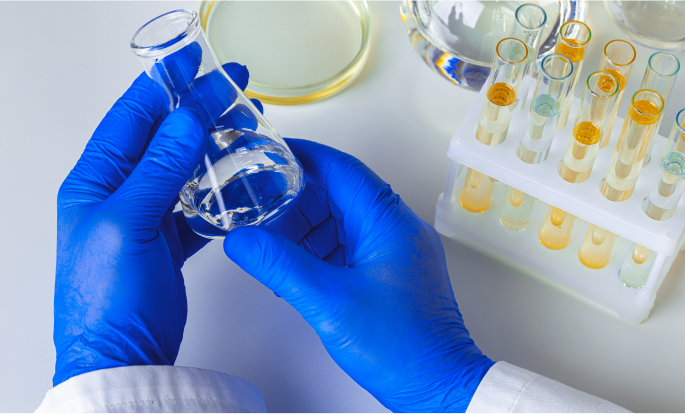
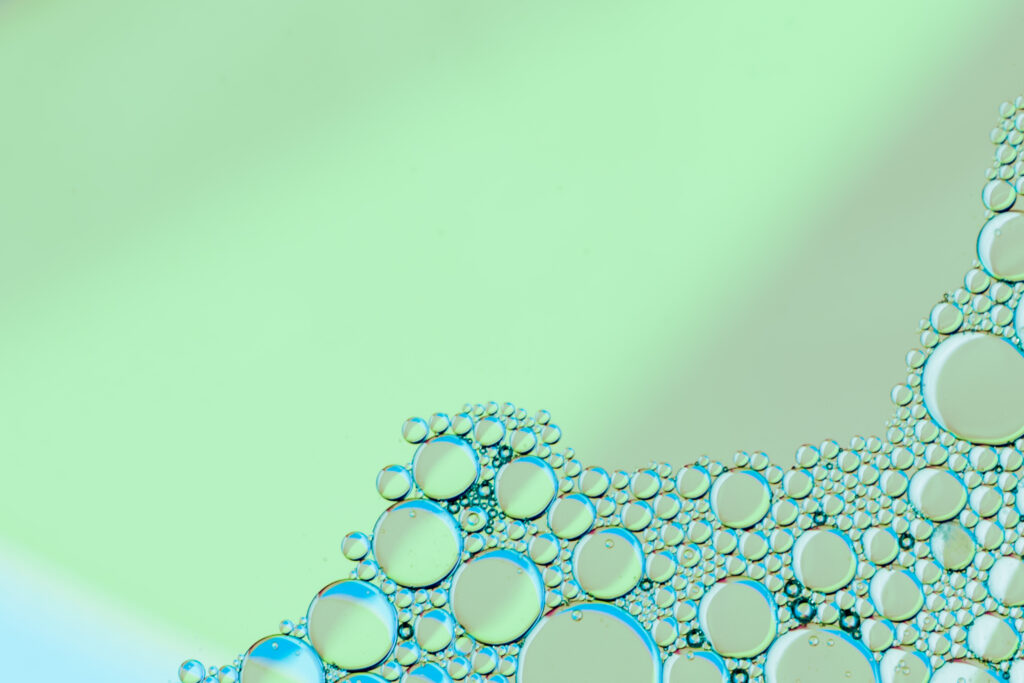
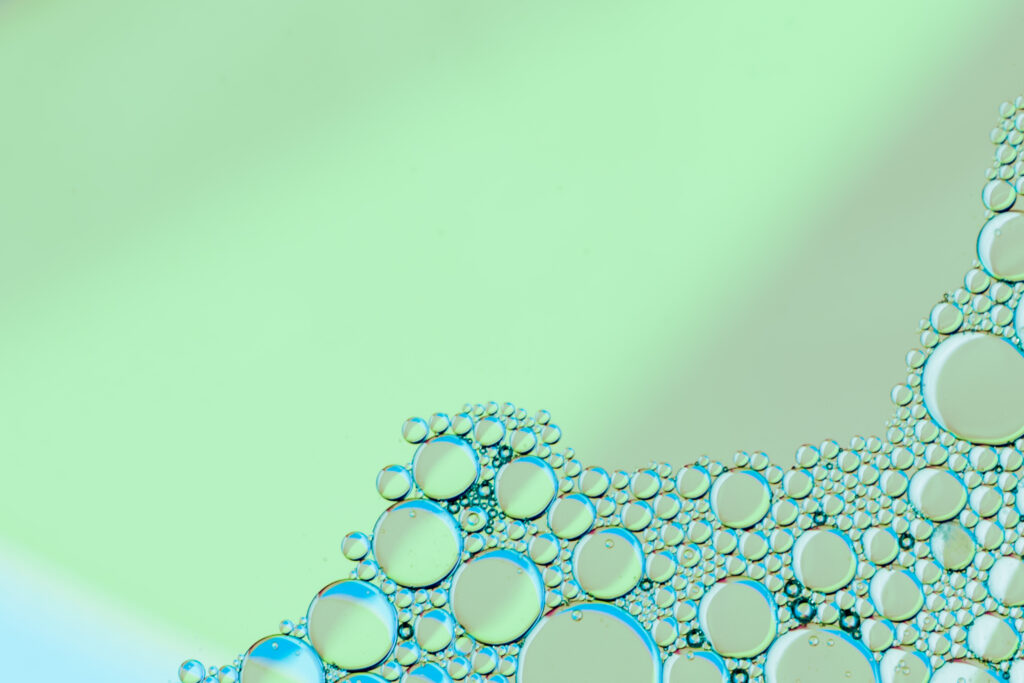
Foam Creation and Chemical Control
Foam is created when gas is dispersed in a liquid, forming bubbles stabilized by surfactants.
Defoamers work by disrupting the surfactant-stabilized bubbles. They spread rapidly across the foamy surface, destabilize the foam film, and cause the bubbles to collapse.
How Defoamers Work
Mechanism of Action
Defoamers work by breaking the surface tension of foam bubbles, causing them to collapse.
They can be surface-active agents that spread rapidly on foamy surfaces or insoluble particles that disrupt bubble formation.
Key Properties
Types of Defoamers
Oil-based Defoamers
Made from oils such as mineral oil, vegetable oil, or silicone oil.
Suitable for various industrial applications, offering good spreading properties.
Water-based Defoamers
These are emulsions containing oils and hydrophobic particles.
They are environmentally friendly and suitable for applications where water solubility is important.
Silicone-based Defoamers
Contains silicone compounds, offering excellent defoaming performance.
Effective in a wide range of temperatures and pH levels.
Non Silicone-based Defoamers
Made from organic and synthetic components excluding silicone.
Suitable for applications where silicone contamination is a concern, such as in paint and coating industries.
Powder Defoamers
Used in dry applications, these are typically silicone or non-silicone-based.
Ideal for powder-based products like cement, detergents, and fertilizers.
Applications of Defoamers
Industrial Defoamers
Crop Protection
Controls foam during pesticide formulation and spraying, ensuring even distribution of active ingredients.
Cleaning Products
Controls foam in industrial and household detergents, enhancing cleaning efficiency and rinsing.
Pulp Processing
Minimizes foam in pulp washing and bleaching, ensuring smooth operation and high-quality paper production.
Prevents foam in aeration tanks and wastewater treatment plants, improving water quality and plant efficiency.
Metal and Glass Working Fluids
Reduces foam in cooling lubricants during machining and grinding, ensuring surface quality and tool life.
Controls foam in drilling fluids and during crude oil separation, maintaining equipment efficiency and safety.
Prevents foam in dyeing and finishing processes, ensuring uniform color and fabric quality.
Chemical Processing
Reduces foam in chemical reactions and distillations, improving yield and process stability.
Eliminates foam during mixing and application, ensuring a smooth, defect-free finish.
Laundry and Dishwashing
Controls foam in automatic washing machines and dishwashers, enhancing cleaning efficiency.
Cement and Concrete Manufacturing
Minimizes foam in concrete admixtures, ensuring uniformity and strength in construction materials.
Biotechnological Processes
Reduces foam in fermentation and cell culture processes, maintaining product yield and purity.
Food Grade Defoamers
Beverage Processing
Prevents foam in fermentation tanks and bottling lines, maintaining product quality and efficiency.
Food Processing
Reduces foam in boiling and frying processes, improving product appearance and process efficiency.
Dairy Processing
Controls foam in milk pasteurization and cheese production, ensuring consistent product quality.
Juice Extraction
Minimizes foam during fruit and vegetable juice extraction, ensuring high juice clarity and yield.
Sugar Production
Prevents foam in sugar crystallization and refining processes, improving purity and processing efficiency.
Brewery Operations
Reduces foam in brewing and fermentation, maintaining product consistency and quality.
Best Practices for Using Defoamers
Selection Criteria
- Choose defoamers based on the specific requirements of the process (e.g., temperature, pH, and medium).
- Consider environmental impact and compliance with regulations.
Dosage and Application
- Determine the correct dosage through small-scale tests.
- Add defoamers at points where foam formation is most likely.
Viscosity Range for Applications
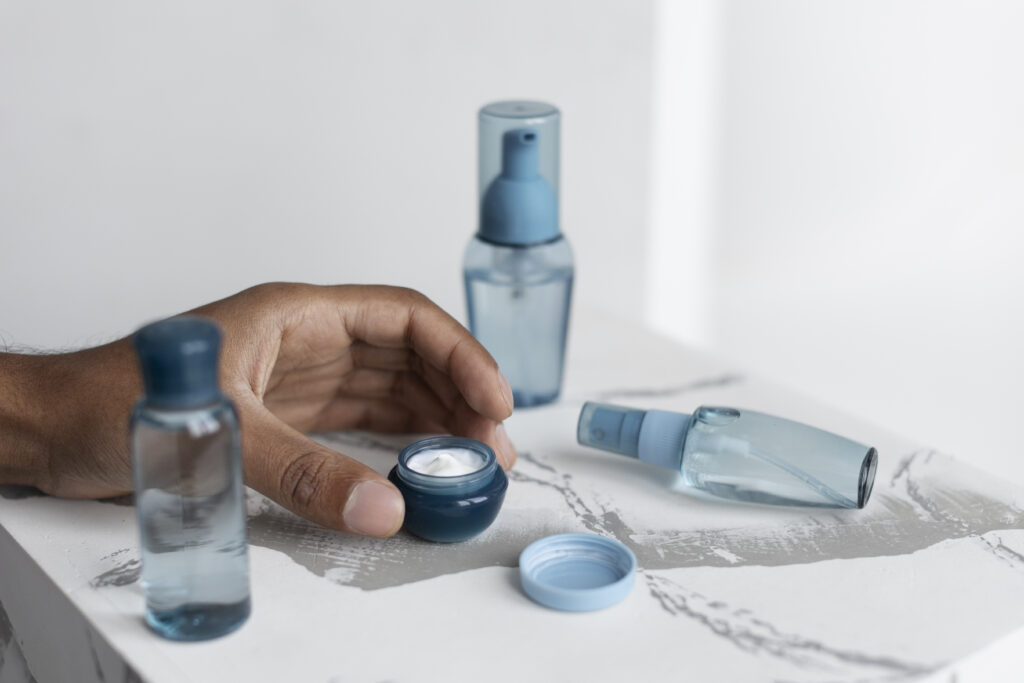
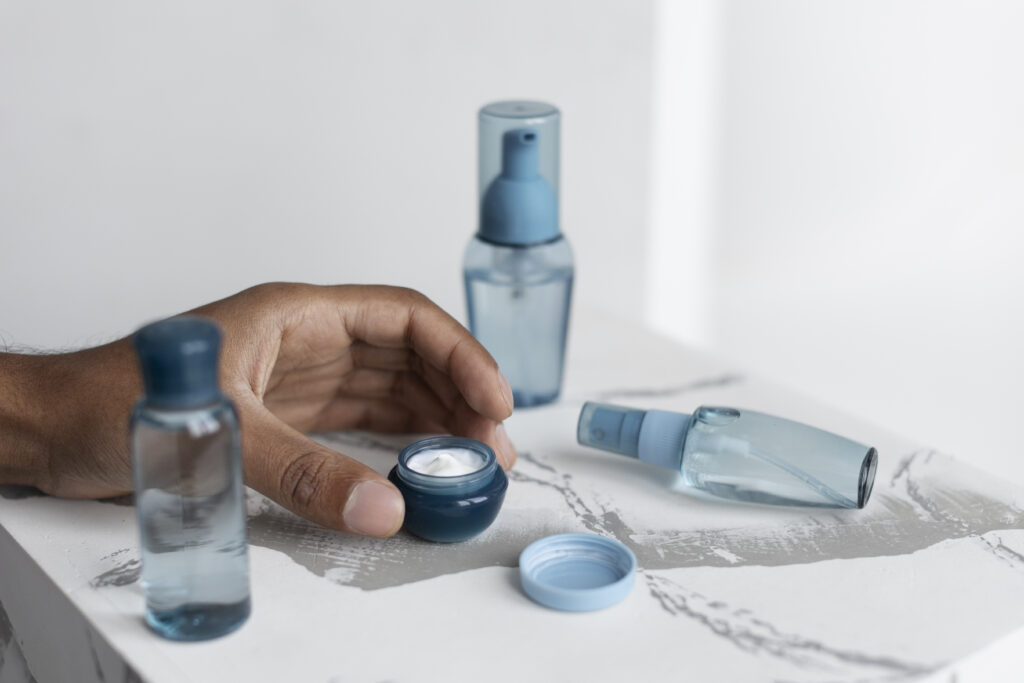
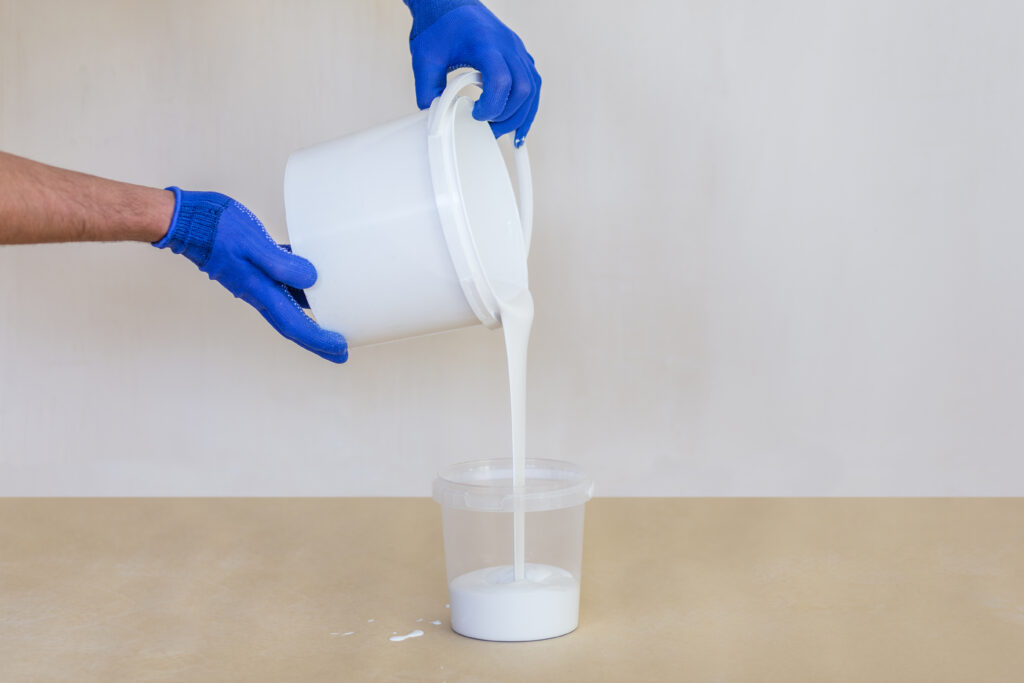
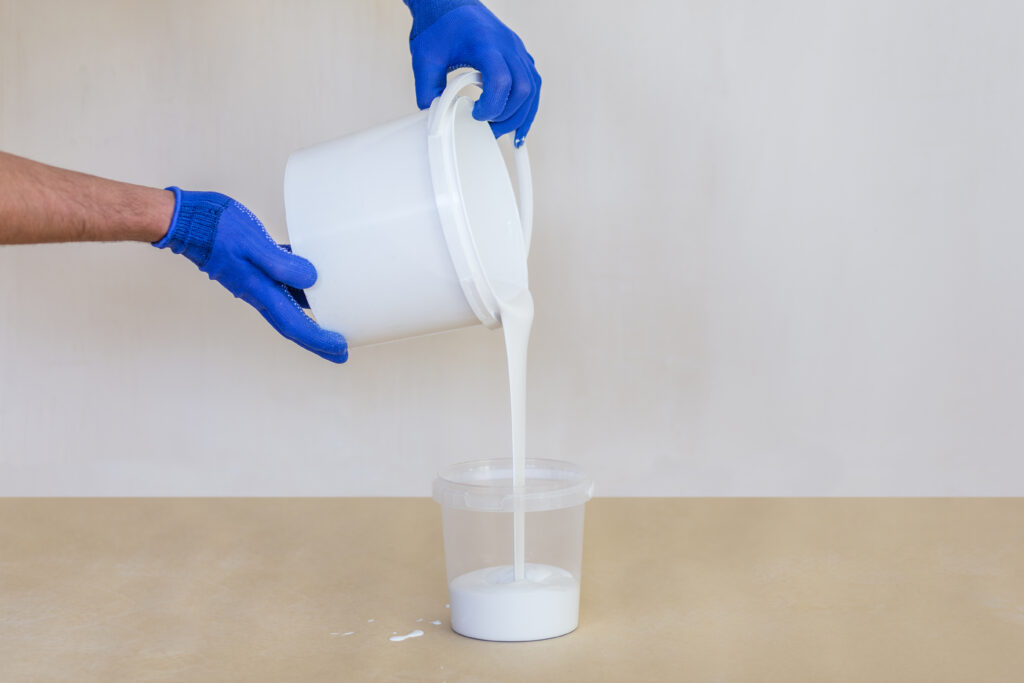
Monitoring and Maintenance
Regularly monitor foam levels and adjust defoamer dosage as needed.
Maintain equipment to ensure optimal defoamer performance.
Environmental and Safety Considerations
Environmental Impact
Select environmentally friendly defoamers when possible.
Ensure proper disposal of defoamer residues.
Safety Precautions
Follow safety data sheets (SDS) for handling and storage.
Use appropriate personal protective equipment (PPE) when handling defoamers.
Effective foam control is essential for various industrial processes.
Understanding the types and applications of defoamers helps in selecting the right product for specific needs.
Future Trends
Effective foam control is essential for various industrial processes.
Innovations in defoamer formulations focus on improving efficiency and environmental sustainability. The development of new materials and technologies will continue to enhance foam control solutions.
Packing, Storage & Transportation
Defoamers are packaged in various sizes to meet different industrial needs, including 50KG, 60KG, 150KG, 200KG, and 1000KG plastic barrels. These packages ensure easy handling, storage, and transportation.
Proper storage conditions include keeping the product in a cool, dry place away from direct sunlight and extreme temperatures to maintain its efficacy and longevity. When transporting, ensure that the barrels are secured to prevent spillage or damage.
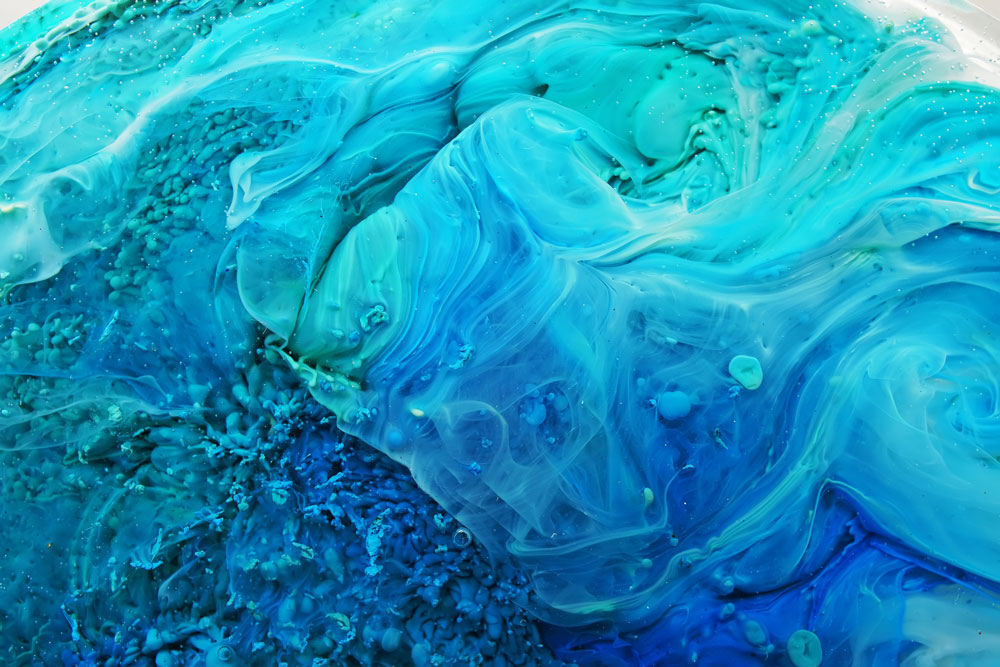
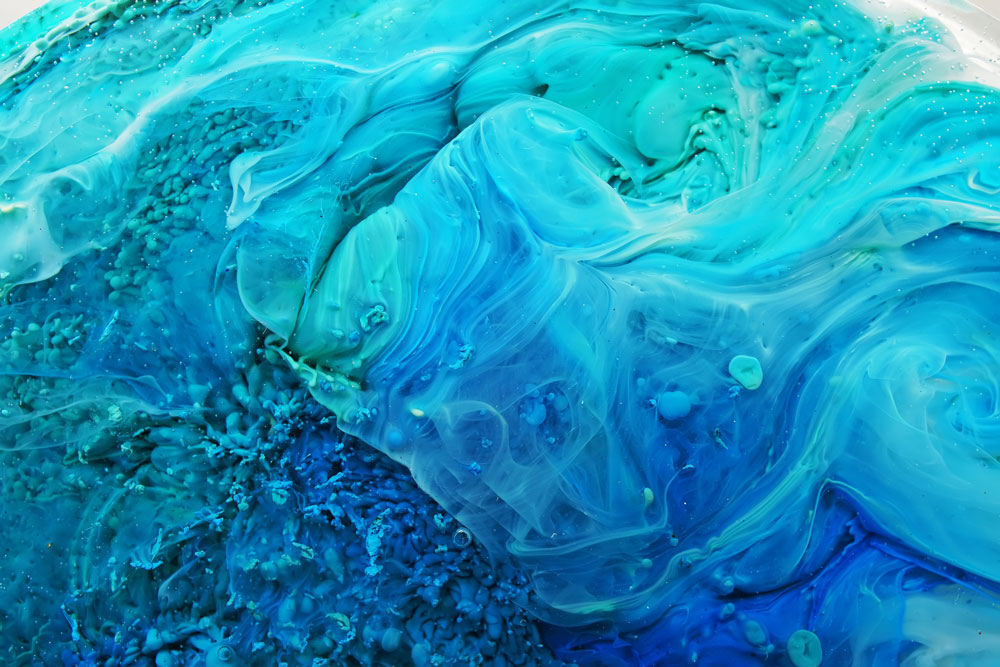
Technical Support and Consulting
We provide comprehensive technical support and consulting services to help you select the right defoamer for your specific needs.
Our team of experts can assist in tailoring defoamer solutions that are optimized for your processes, ensuring maximum efficiency and effectiveness.
Whether you need assistance with product selection, application techniques, or troubleshooting, we are here to support you every step of the way.
Benefits of Buying from Us
- Quality Assurance: We guarantee the highest quality defoamers that meet industry standards and perform reliably in various applications.
- Tailored Solutions: Our defoamers are customized to suit specific industrial and food-grade needs, ensuring optimal performance.
- Expert Support: Benefit from our technical support and consulting services to ensure you get the best defoamer solution for your needs.
- Flexible Packaging: Choose from a range of packaging options to suit your requirements, ensuring easy storage and transportation.
- Competitive Pricing: We offer competitive prices without compromising on quality, providing you with the best value for your investment.
By choosing our defoamers, you ensure high efficiency and reliability in your processes, backed by expert support and tailored solutions.
Standards
Meets ASTM D1173 standards for silicone defoamers.